Are you struggling to decide which wheel loader bucket size is right for your needs? Selecting the incorrect size can cause inefficiencies, safety risks and unnecessary costs. Imagine overloading your machine, which leads to frequent breakdowns or using a bucket too small, which doubles your workload.
To select the ideal wheel loader bucket size, it’s essential to evaluate key factors such as material properties, loader specifications and project requirements. By carefully considering these aspects, you can make a more informed decision and optimize your loader’s performance.
This guide offers practical insights to help you choose the right wheel loader bucket size. Let’s explore the key considerations and tips for choosing the ideal wheel loader bucket size for your projects.
Table of Contents
ToggleWhat is Wheel Loader Bucket?
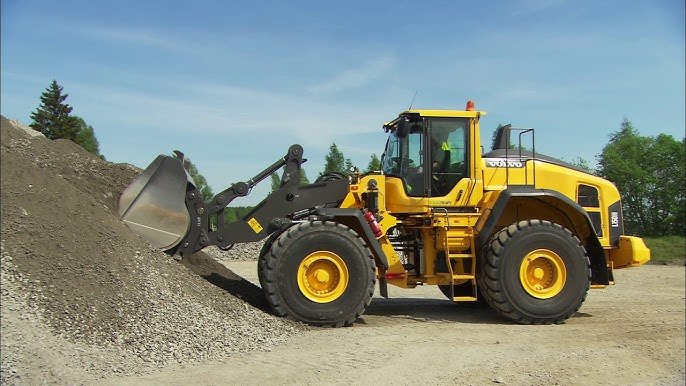
A wheel loader bucket is an attachment mounted to the front of a wheel loader, specifically designed for material handling tasks. It is the most essential tool for loaders and plays a crucial role in determining the efficiency and versatility of the equipment.
The wheel loader bucket is the key attachment for material handling, ranging from construction debris to agricultural produce. Its design and size directly affect performance.
The design of a wheel loader bucket is tailored to its purpose. General-purpose buckets are perfect for basic tasks like moving soil, sand or gravel, while specialized buckets such as rock or grapple buckets handle specific materials. Modern buckets often include wear-resistant materials and teeth for improved durability and performance. These features enable buckets to withstand harsh conditions, making them indispensable in construction, mining and agricultural industries.
Buckets attach to loaders via hydraulic arms, allowing operators precise control over lifting and dumping motions. The bucket’s geometry, including width, height and depth, determines its capacity and the type of material it can handle. Properly maintaining the bucket is vital to prolong its life and prevent costly downtimes, especially when used in demanding environments.
What Are Wheel Loader Bucket Type and Function?
Choosing the correct wheel loader bucket type is essential for improving efficiency on your job site. Different wheeled loader buckets are designed for specific materials and tasks and understanding the unique functions of each type will help you make the right choice. Selecting the right bucket wheel loader attachment ensures that your loader can handle the demands of your work while minimizing wear and tear on the equipment.
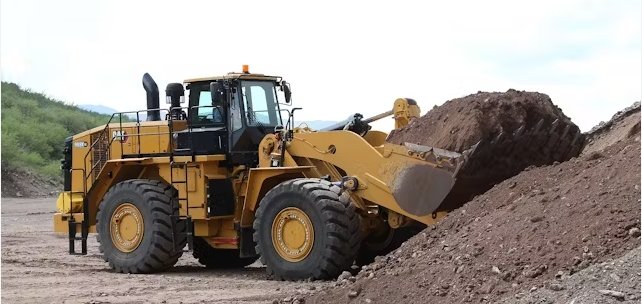
Wheel loader bucket types like front loader buckets, heavy equipment buckets and compact wheel loader bucket designs all have different functions. Understanding these variations will guide you toward the most suitable bucket for your project.
General Purpose Bucket
The general purpose front loader bucket is versatile, ideal for handling light materials like dirt, gravel and sand. It’s the most commonly used wheel loader bucket due to its balanced wheel loader bucket capacity and efficiency in everyday construction and landscaping applications.
Wheel Loader Light Material Bucket
For light, fluffy materials such as snow, mulch or sand, the light material bucket has a larger volume with a shallow depth. This design increases the wheel loader bucket capacity without adding unnecessary weight, making it perfect for jobs like snow removal or landscaping, especially for those using compact wheel loader buckets.
Wheel Loader Heavy-Duty Bucket
The heavy-duty bucket is reinforced to handle dense, tough materials like rock or concrete. With extra-strength steel, it’s ideal for bucket wheel loader operations or heavy-duty construction tasks, including quarrying and mining. If you’re working with abrasive materials, the wheel loader bucket teeth help increase the bucket’s lifespan.
Wheel Loader Rock Bucket
Designed for moving large rocks or other rugged materials, the rock bucket features reinforced edges and high-tensile steel, making it perfect for heavy equipment buckets in quarries and mining operations. The compact wheel loader bucket version is often used in smaller operations or where access is limited but rock handling is still required.
Wheel Loader Fork Bucket
The fork bucket, also known as a clamshell bucket, combines a traditional bucket with forks, allowing for precise material handling such as pallets or logs. It’s commonly used in material handling tasks requiring accuracy, making it perfect for industries that use heavy equipment buckets for lifting bulky items.
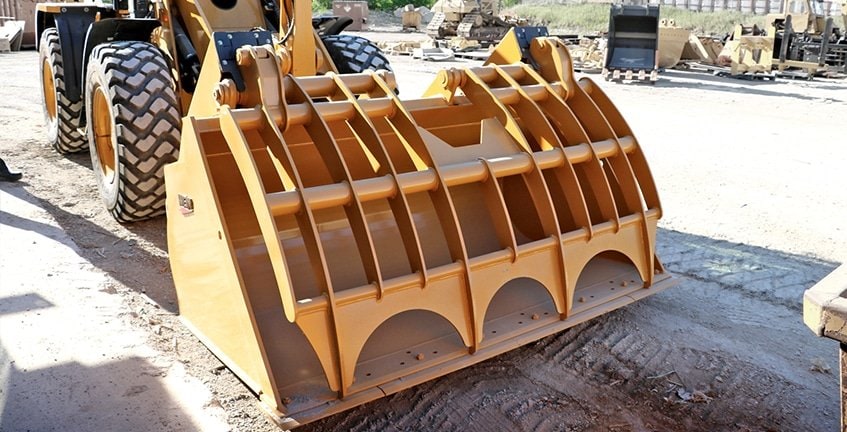
Wheel Loader Waste Bucket
The waste bucket is designed for debris and scrap material, featuring a smooth, flat-bottomed design that’s ideal for handling construction or demolition waste. It’s particularly useful when handling mixed waste materials and can be found in operations where wheel loader bucket teeth are needed to assist with material scraping and collection.
Wheel Loader High Capacity Bucket
The high-capacity wheel loader bucket is designed to move large volumes of material in one scoop. Its larger size increases efficiency, especially for bucket wheel loader operations that deal with large-scale projects. However, ensure your loader has the necessary lifting capacity to handle the extra load, as the wheel loader bucket size and weight will impact your machine’s performance.
Custom Wheel Loader Buckets
For specialized tasks, custom wheeled loader buckets can be tailored to meet unique needs, such as handling specific materials or providing additional features like wear-resistant edges or special teeth. Whether it’s a custom front loader bucket or a specially designed heavy equipment bucket, these buckets help increase efficiency in tasks that require customized solutions.
Why is Choosing the Right Wheel Loader Bucket Size So Important?
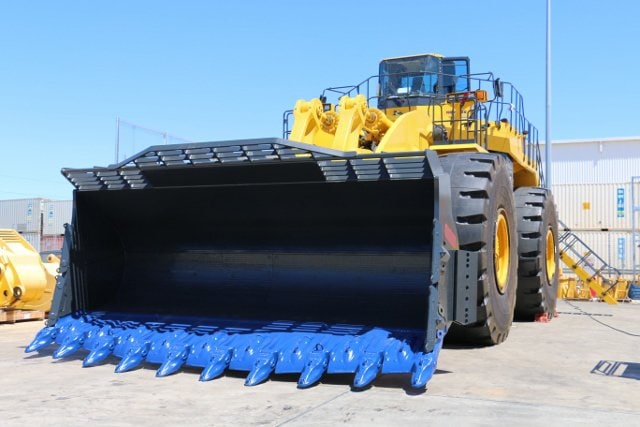
Selecting the right wheel loader bucket size plays a crucial role in maximizing your loader’s performance. If you choose a bucket that’s too small, you’ll find yourself making more trips and increasing cycle time. On the other hand, a bucket that’s too large can overburden your loader, causing unnecessary strain on the engine, hydraulic system and drivetrain. Understanding the importance of size selection is key to ensuring that your machine works efficiently and safely, while reducing fuel consumption and maintenance costs.
Choosing the correct wheel loader bucket size optimizes performance, improves fuel efficiency and prevents overloading. It ensures that your loader handles tasks with minimal strain and maximum productivity.
The bucket size determines how much material your wheel loader can handle in one scoop. The right bucket size maximizes wheel loader bucket capacity, reducing the number of cycles needed to complete a task. If you choose a bucket that’s too large for your loader, you may risk overloading the machine, leading to engine strain and unnecessary wear on the components. Furthermore, if you consistently operate with an oversized bucket, the increased fuel consumption will offset any potential productivity gains.
On the other hand, a bucket that is too small can cause the loader to make more trips, increasing cycle times and lowering overall productivity. For example, when handling light materials such as mulch or sawdust, a larger bucket with more volume is ideal because it reduces the number of cycles required to fill a truck or container. For heavy, compacted materials like soil or rocks, you’ll want to choose a smaller bucket that fits your loader’s specifications, ensuring optimal performance without risking overloading.
It’s also important to match the wheel loader bucket size to the material density. Heavy equipment buckets are usually designed to handle dense materials, while light material buckets can manage bulkier, less dense substances. Assessing the material properties can help you determine the best size for the job. If you’re working in a confined space, a smaller compact wheel loader bucket may be a better choice for maneuverability, whereas larger buckets are ideal for open, expansive work sites where loading efficiency is key.
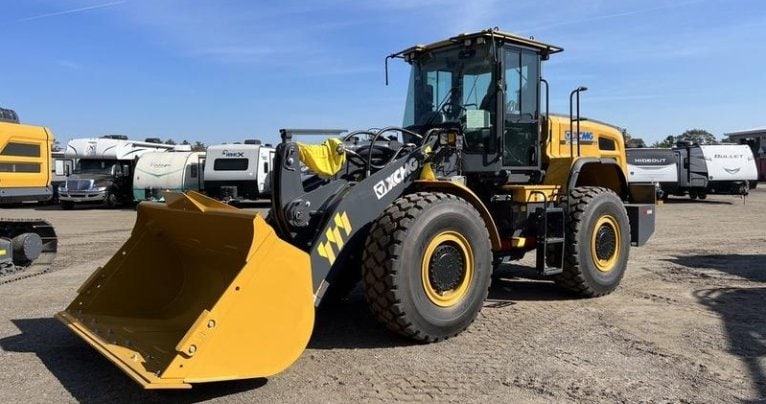
Bucket wheel loader capacity also impacts the machine’s stability. Operating with an over-sized bucket can reduce the loader’s tipping load, which may compromise safety. Always check the loader’s maximum rated capacity and adhere to manufacturer guidelines to avoid tipping risks and ensure safe operation.
Selecting the right bucket size ensures that your wheel loader works within its optimal limits. By balancing size, capacity and material type, you’ll reduce downtime, improve efficiency and extend the lifespan of both the loader and its attachments.
How to Choose the Right Wheel Loader Bucket Size for Your Project?
Choosing the right wheel loader bucket for your project is not just about size; it involves considering a variety of factors such as the material you’re handling, the working environment and the specific tasks you need to perform. Each project comes with its own unique set of demands, so it’s essential to evaluate your options carefully. By matching the bucket type and size to the job requirements, you’ll ensure that your loader works efficiently, safely and economically.
To choose the right wheel loader bucket for your project, consider material type, bucket capacity and job-specific tasks. Matching these elements ensures optimal performance and productivity.
Material Type:
- Light Materials (Sand, Mulch, Snow):
When working with light and loose materials such as sand, mulch or snow, a larger wheel loader bucket size can significantly increase efficiency. Compact wheel loader buckets or general-purpose buckets with higher capacities are ideal for these types of materials. Since the material is light and doesn’t take up much weight per unit of volume, a larger bucket can handle more material with each scoop, reducing the number of trips and cycles needed to complete the job. For example, using a larger front loader bucket for snow removal or landscaping tasks can speed up the process by moving bulk materials faster. - Heavy Materials (Rock, Concrete, Gravel): When dealing with heavier materials like rock, concrete or gravel, the right wheel loader bucket size is crucial to avoid overloading the loader and putting unnecessary strain on the machine. For these dense, compact materials, smaller, more durable heavy equipment buckets with reinforced edges and teeth are typically required. These buckets are designed to handle tough materials and prevent wear on the machine, especially when materials are particularly abrasive or have sharp edges, like rocks.
- Loose, Dry or Powdery Materials (Dirt, Soil, Coal): Materials like dirt, soil or coal have different characteristics compared to sand or rocks. They’re typically more compact than light materials but less dense than rocks, requiring a balanced approach when selecting the right wheel loader bucket size. For dirt and soil, you need a wheel loader bucket that has enough capacity to handle a high volume of material but not so large that it risks spilling or losing material during transport.
- Specialized Materials (Scrap Metal, Timber, Hazardous Waste): For specialized materials like scrap metal, timber or hazardous waste, you’ll need a bucket that is designed to handle these unique challenges. Heavy equipment buckets with additional durability and specialized features, such as hydraulic grippers or reinforced edges, are commonly used for these types of materials. When working with scrap metal, for instance, you may need a front loader bucket with increased capacity to handle the volume of metal, while also ensuring that the materials don’t damage the bucket or loader. Specialized buckets designed for wheel loader bucket teeth and durability are essential when handling such materials.
Wheel Loader Bucket Capacity:
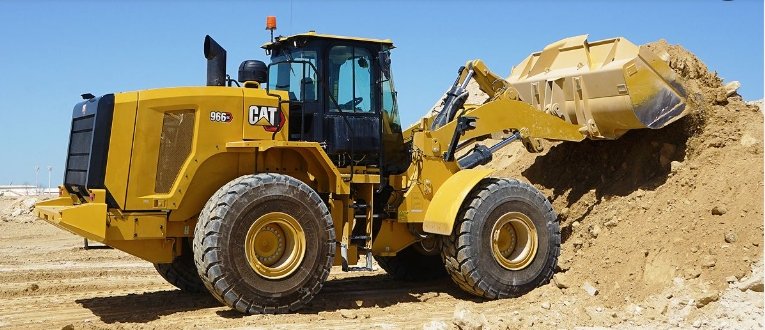
Another critical factor when choosing a wheel loader bucket is its capacity. Your project’s scale will help determine the ideal capacity. If you’re working on a large-scale construction or mining project, a wheel loader bucket with a larger capacity may be the best option. A bucket wheel loader designed for higher volume can reduce the number of cycles needed to complete the job, improving productivity. However, it’s essential not to exceed the loader’s rated capacity, as this could compromise its performance and safety. For smaller tasks or more confined spaces, a compact wheel loader bucket may be a better option, offering more precise control and improved maneuverability.
Matching the right wheel loader bucket capacity with the loader’s capabilities ensures that the machine works efficiently, while also preventing strain on the hydraulic system, engine and drivetrain. Remember, operating a bucket that exceeds the machine’s capacity can lead to excessive fuel consumption, overheating and even premature breakdowns.
Wheel Loader Bucket Design and Features
The design of your wheel loader bucket also plays a significant role in selecting the right bucket for your project. For example, wheel loader bucket teeth are essential for digging into compact or rocky materials. If you’re working in a rough environment, you may want a bucket with reinforced teeth or a specialized cutting edge. Heavy equipment buckets are often designed with additional wear-resistant materials to handle tough materials like gravel, asphalt and stone. These durable features extend the lifespan of your bucket and reduce the need for frequent maintenance.
Additionally, bucket design can affect your machine’s efficiency in terms of material handling. A well-designed bucket that provides optimal material flow and unloading capabilities will speed up the overall process. For tasks like grading or pushing loose material, a front loader bucket with specific features may be ideal, as it provides stability and control.
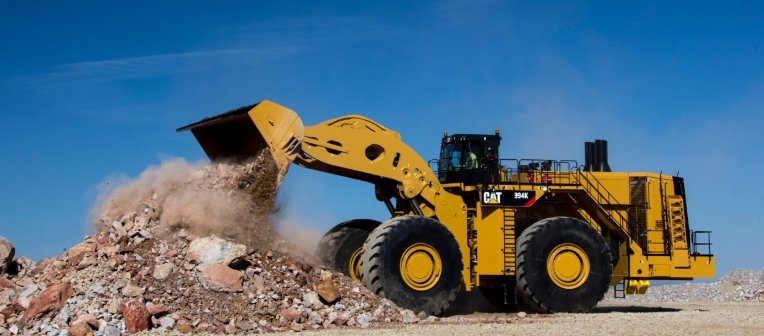
Wheel Loader Buckets Working Environment
Consider the working conditions where your wheel loader will be operating. Will you be working in confined spaces or open areas? For tight workspaces, a compact wheel loader bucket offers more maneuverability, allowing you to work in restricted areas with precision. On the other hand, if you’re working in an open area with no constraints, a larger, higher-capacity bucket will help you handle materials more efficiently.
The terrain is also a key factor to consider. If you’re working on rocky or uneven ground, a bucket wheel loader with a low profile and heavy-duty design might be necessary to handle the demanding conditions. Always ensure that the bucket you choose is compatible with the environmental conditions to prevent unnecessary wear and maximize performance.
Loader Compatibility
Finally, you need to ensure that the wheel loader bucket you select is compatible with your loader. Consider the loader’s model and its maximum bucket wheel loader capacity. Not all buckets fit all loaders, so you’ll want to choose a bucket that’s designed for your specific machine to ensure proper fitment and optimal performance. Using a bucket that’s too large for your loader can lead to stability issues, while a bucket that’s too small may not provide enough material handling capacity to complete the job efficiently.
What Are Common Mistakes to Avoid When Choosing a Wheel Loader Bucket Size?
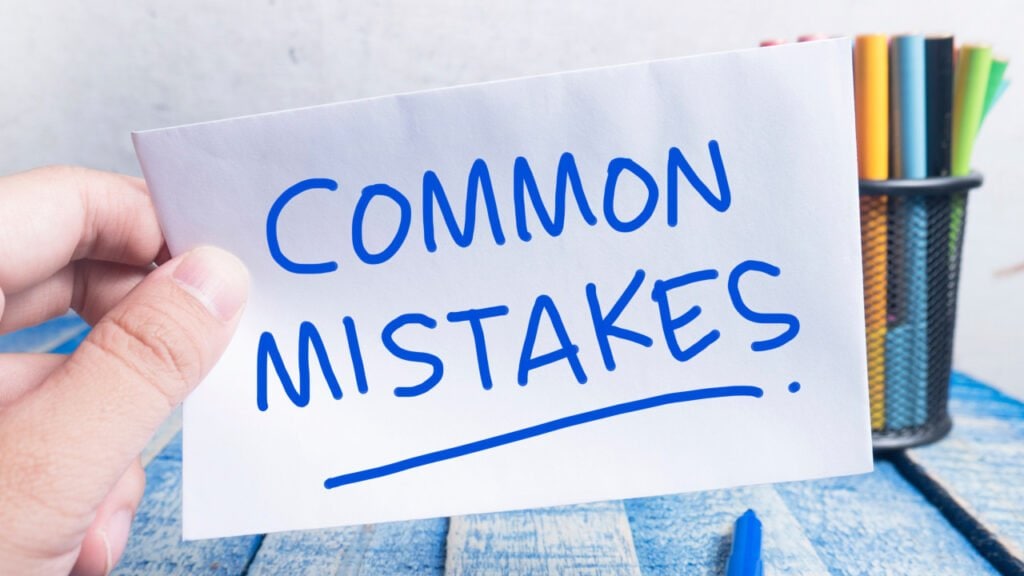
Selecting the right wheel loader bucket size is crucial for ensuring efficiency and preventing unnecessary wear. However, there are several common mistakes you should avoid when making your choice. By being aware of these, you can improve your machine’s performance and longevity.
Choosing the Wrong Bucket Size for the Material
When selecting a wheel loader bucket, always match the size to the material you’re handling. If you choose a bucket that’s too large for light materials like sand or gravel, you may find that the bucket doesn’t fill efficiently, causing more passes to complete the task. For heavier materials like rock or concrete, using a smaller front loader bucket is better as it prevents overloading your machine.
When you’re using a bucket wheel loader, the key is to ensure the bucket is optimized for the specific material. Wheel loader bucket size should align with the material density to improve productivity.
Ignoring the Machine’s Hydraulic Capacity
Overloading your wheel loader by selecting a bucket too large for the machine’s hydraulic capacity can cause major performance issues. This strain can lead to slower bucket lifting, potential overheating or even system failure. Always ensure that the bucket size fits within the hydraulic capabilities of your loader. If you are using a larger bucket wheel loader, you’ll likely have the capacity to handle a bigger bucket with more volume, but smaller loaders might need a compact wheel loader bucket that matches their hydraulic limits.
Disregarding the Loader’s Stability
A common mistake is choosing a wheel loader bucket that is too large for your machine, which compromises its stability. This can make the loader top-heavy and prone to tipping, especially when handling heavy loads. If you’re working with a larger front loader bucket, make sure it’s suitable for your machine’s weight and stability. For smaller loaders, opt for a smaller wheel loader bucket size to maintain a balanced, safe operation.
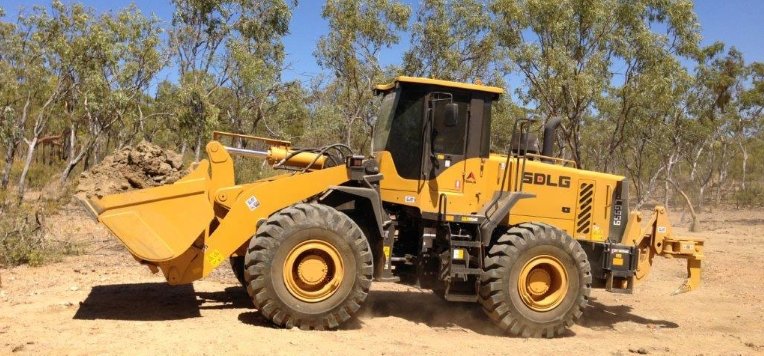
Choosing an Incompatible Bucket
Not all buckets are compatible with every wheel loader. Make sure the wheel loader bucket you choose is designed for your specific machine. Some loaders require specific pin sizes or attachment systems. Using a heavy equipment bucket that doesn’t fit your loader’s attachment system can result in mechanical issues, inefficient performance or even damage to your machine. Double-check compatibility to avoid unnecessary downtime or repairs.
Overlooking Long-Term Maintenance Needs
Larger buckets, especially wheel loader buckets with teeth, tend to experience more wear and tear. If you’re frequently working with abrasive materials, like gravel or crushed rock, the bucket wheel loader might need more frequent maintenance. A smaller compact wheel loader bucket may wear less quickly, but it could result in more cycles to complete the same amount of work. Balance bucket size and long-term maintenance needs to avoid costly repairs and downtime.
Neglecting the Loader’s Reach and Dumping Height
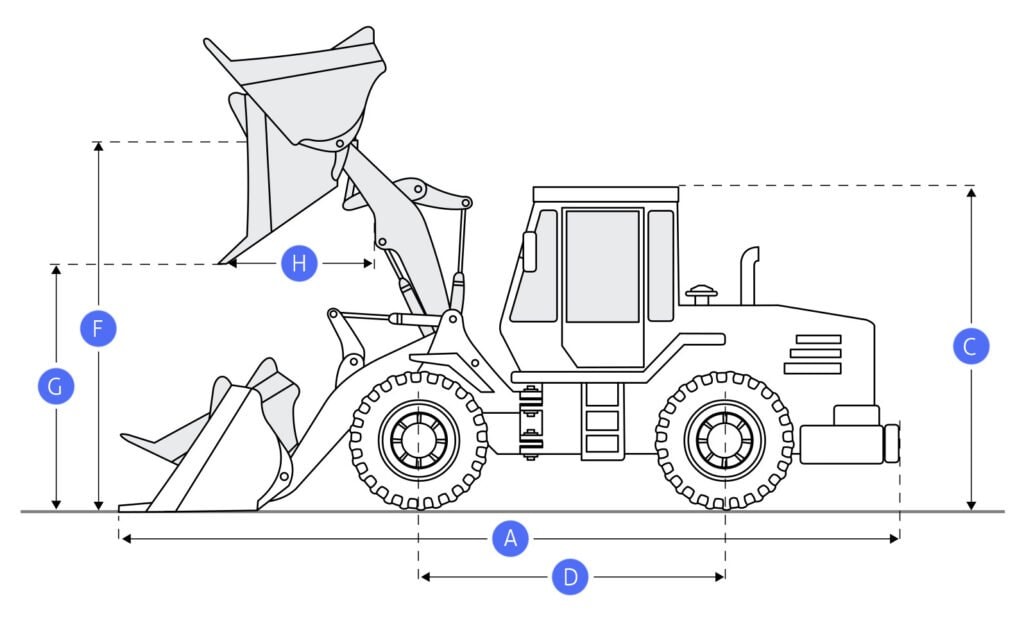
Ensure that your wheel loader bucket size is suited to your loader’s dumping height and reach. A larger bucket that exceeds your machine’s dumping height can lead to inefficient unloading, as material may spill over or take more time to dump. If you’re working with a loader that has a limited reach, choosing a front loader bucket or a smaller wheel loader bucket ensures better efficiency during unloading, especially when dumping into high-sided trucks or stockpiles.
Summary
Choosing the right wheel loader bucket size is crucial for maximizing your machine’s efficiency and performance. By avoiding common mistakes such as mismatching bucket size with material type, overlooking hydraulic capacities or ignoring machine stability, you can ensure smoother operations and lower maintenance costs. If you’re unsure which wheel loader bucket size is best for your needs, don’t hesitate to contact us at Hiosen Machinery. Our team is here to help you select the perfect bucket to match your loader’s specifications and your operational requirements. Let us assist you in optimizing your equipment for maximum productivity.